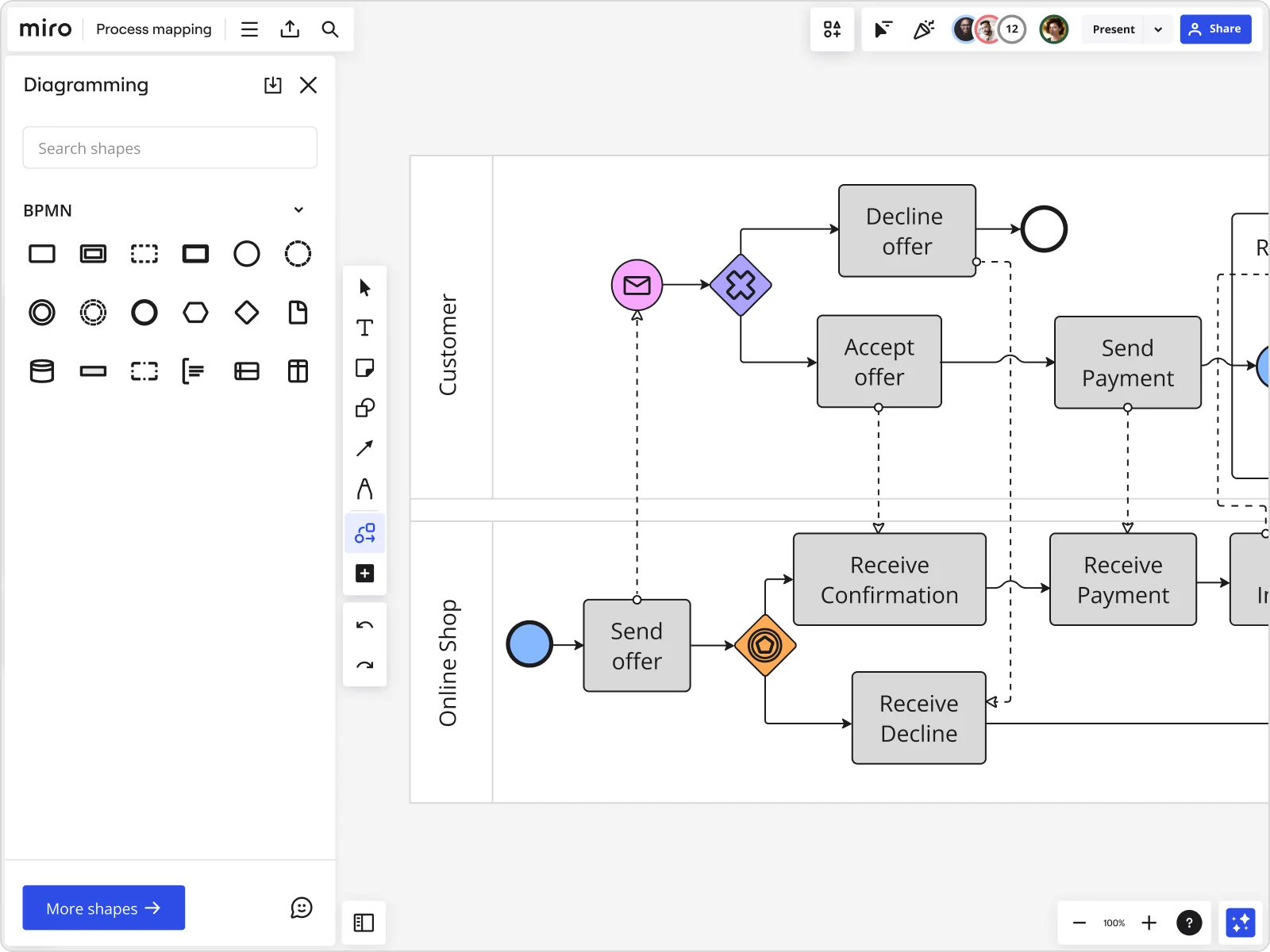
Process improvement methodologies
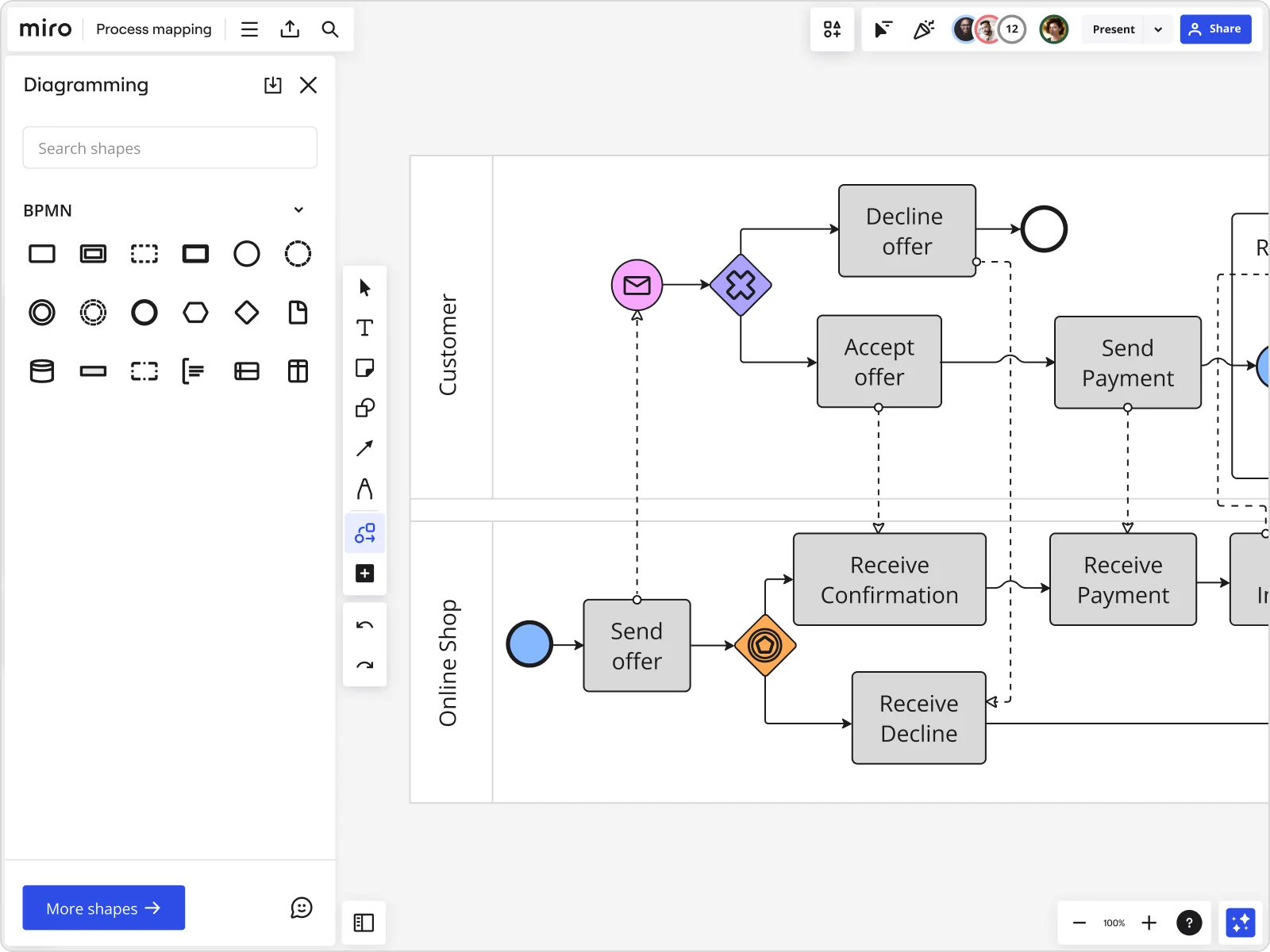
Process improvement represents a strategic approach that examines business workflows to foster efficiency, competitiveness, and profitability. In modern economic challenges, businesses must prioritize efficiency through systemic, continuous improvements.
This guide delves into businesses' core process improvement methodologies to drive operational efficiency. With in-depth understanding and application, these methodologies can unlock higher levels of productivity, customer satisfaction, and business growth.
What is process improvement?
At its core, process improvement entails a systematic review and refinement of business operations. It aims to identify, analyze, and improve existing business processes to optimize performance, meet best practice standards, or enhance key business metrics such as cost, quality, service, and speed.
Role of process improvement in businesses
Process improvement plays dual roles in an organization. Firstly, as a proactive measure, it ensures operational excellence by cultivating a culture of continuous improvement. This encourages businesses to constantly reevaluate their workflows, pinpointing areas of potential optimization. This proactive approach enhances efficiency, effectiveness, and agility in fluctuating market conditions.
On the other hand, as a reactive measure, process improvement can fix operational issues and mitigate potential risks. Process improvement methodologies offer tools for systematic, data-driven problem diagnosis and resolution in cases of productivity bottlenecks, quality mishaps, or customer dissatisfaction. This reactive capability is crucial for maintaining operational resilience and guaranteeing customer satisfaction.
Benefits of process improvement practices
Implementing process improvement methodologies can deliver various benefits. At the operational level, it can streamline workflows, minimize waste, lower costs, and elevate quality standards. At a strategic level, it can heighten organizational agility, foster innovation, and establish a continuous learning and development culture. It can bolster profit margins and enhance shareholder value from a financial perspective.
Factors to consider before implementing process improvement
Before diving into process improvement, several factors warrant careful consideration. The choice of an appropriate methodology should be informed by the organization's unique circumstances, such as the nature and complexity of its processes, the extent of improvement sought by the existing organizational culture, and the available resources.
It's also worth noting that process improvement is a long-term endeavor rather than a one-time project. It requires sustained commitment from all organizational levels, frequent revisiting and revision of processes, and a readiness to question and redefine the status quo.
Challenges in process improvement
Process improvement, while replete with benefits, is not devoid of challenges. Resistance to change, inadequate leadership commitment, resource limitations, and difficulties quantifying success are common hurdles. Navigating these obstacles necessitates a strategic approach, strong leadership, effective communication, comprehensive training, and ongoing support.
In recap, process improvement forms the backbone of business growth, competitiveness, and sustainability. It's an inseparable component of business strategy and operations, marking the difference between thriving and surviving in today's vibrant business landscape.
Examples of process improvement methodologies
There are several process improvement methodologies that organizations use to enhance efficiency, effectiveness, and overall performance. Here are some notable examples:
Six Sigma
Six Sigma is a data-driven methodology that strives to eliminate defects and reduce process variability. Central to Six Sigma is the DMAIC approach (Define, Measure, Analyze, Improve, Control), which provides a structured framework for problem-solving. Miro's DMAIC analysis template is a great example.
Motorola is an excellent example of Six Sigma's success. Since its implementation in the 1980s, Motorola reported savings of $17 billion by 2006, largely attributed to its Six Sigma program.
Lean
Rooted in the Toyota Production System, Lean focuses on waste reduction to improve overall customer value. The 5S system (Sort, Set in order, Shine, Standardize, Sustain) forms the heart of Lean, ensuring workspace optimization and waste minimization.
Toyota's success story underpins the efficacy of Lean. Through this approach, Toyota dramatically reduced waste and improved productivity, resulting in global leadership in the automotive industry.
Try Miro's Lean Six Sigma templates.
Total Quality Management (TQM)
TQM is a management framework committed to long-term success through customer satisfaction. It encompasses all members of an organization, from management to frontline staff, in improving processes, goods, services, and culture.
The Federal Express (FedEx) Corporation, an American courier company, is a classic example of successful TQM implementation, having seen consistent growth and customer satisfaction rates.
Business Process Re-engineering (BPR)
BPR involves radical redesigning of core business processes to achieve substantial improvements in productivity, cycle times, and quality. While promising dramatic improvements, BPR also comes with a set of implementation challenges, such as resistance to change.
Hallmark, the renowned greeting card company, utilized BPR to transform its product development process, reducing the cycle time by 50%.
Kaizen
Kaizen, a Japanese philosophy that means 'change for the better,' focuses on continuous, incremental improvement. Central to Kaizen is the Suggestion System, where all employees are encouraged to propose small improvements.
Toyota's implementation of Kaizen, apart from Lean, also contributed to its rise as a global automotive leader, showcasing the importance of employee engagement in continuous improvement.
Implementing process improvement methodologies
Implementing process improvement methodologies involves a well-thought-out, systematic approach. The journey typically begins with a thorough understanding of the current processes, identifying inefficiencies, and pinpointing areas for improvement. This is followed by setting specific, measurable, achievable, relevant, and time-bound (SMART) goals to guide improvement.
Once these foundational steps are complete, the selected methodology is implemented. The steps may vary depending on the methodology used, but they generally involve planning and design, implementation, monitoring, and control. It's crucial to document every stage, making it easier to analyze results and make necessary adjustments.
Role of leadership in process improvement
Leadership plays an indispensable role in process improvement. Leaders set the vision and strategic direction for process improvement efforts and create an environment that nurtures innovation and accepts change. They must champion the process improvement initiative, providing motivation, resources, and support to the teams involved.
In addition, leaders are responsible for managing resistance to change, a common challenge in process improvement initiatives. They need to communicate the reasons for the change, its benefits, and how it aligns with the overall business strategy ensuring organizational buy-in.
Training and support for employees
Employee training and support are pivotal to successful process improvement. Training equips employees with the necessary knowledge and skills to apply process improvement methodologies effectively. This training can take various forms, from formal educational programs to on-the-job training and mentoring.
Conversely, support is about providing employees with the necessary resources and tools to carry out their tasks efficiently. It also involves creating a supportive culture that encourages employees to contribute ideas, voice concerns, and actively participate in process improvement initiatives.
Monitoring and measuring success
Monitoring the implementation of process improvement methodologies is crucial for ensuring they are on track to achieving the set goals. This involves regularly reviewing the progress, measuring performance against established metrics, and making necessary adjustments in your process map.
Measuring success is an integral part of this monitoring process. It helps ascertain whether the process improvement initiative is delivering the expected results. The measurements can be quantitative, like cost savings or time reductions, or qualitative, like improved customer satisfaction or employee morale.
Successful process improvement relies on a systematic approach, strong leadership, adequate training, and consistent monitoring. These elements, when effectively implemented, can lead to significant enhancements in business efficiency and productivity.
The future of process improvement
As we look forward, several emerging trends are set to reshape the landscape of process improvement. One key trend is the increasing emphasis on sustainability. More businesses are integrating green practices into their process improvement efforts, aiming to reduce waste and environmental impact while improving efficiency.
Another trend is the growing focus on customer experience. Process improvement initiatives are increasingly designed to enhance customer satisfaction and loyalty, reflecting a shift from internal to external process orientation.
Additionally, the concept of Agile process improvement is rising. This approach values flexibility, responsiveness, and incremental improvements, moving away from the traditional 'big bang' style of large-scale, one-time changes.
The role of technology in process improvement
Technology and digitization are significant drivers of change in process improvement. Artificial intelligence, machine learning, and automation tools are employed to identify patterns, predict trends, and recommend improvements. They are helping businesses optimize processes in real time, leading to significant savings in cost and time.
Also, technologies such as blockchain and the Internet of Things (IoT) provide unprecedented transparency and connectivity, opening up new opportunities for process improvement. For instance, blockchain can enhance process integrity and security. At the same time, IoT can help track and optimize resource utilization in real time.
Adapting to new methodologies
Adapting to new methodologies and techniques is a must in the evolving world of process improvement. Businesses must stay up-to-date with the latest research and trends in process improvement and continuously upskill their employees. This includes not just technical skills but also soft skills like change management, problem-solving, and creativity, which are essential for navigating the complexities of process improvement.
Moreover, businesses must foster a culture of learning and innovation, encouraging employees to experiment with new ideas and learn from failures. This culture of experimentation and learning is a crucial enabler for continuous process improvement.
The future of process improvement is both exciting and challenging. It promises new opportunities for efficiency and growth, driven by technological advancements and new thinking. However, it also demands that businesses be adaptive, agile, and continually learn. By embracing these changes and staying ahead of the curve, companies can turn process improvement into a significant competitive advantage.
Apply process improvement methodologies in Miro
Mastering process improvement methodologies is an invaluable skill set for modern businesses. As tech continues to evolve and competition gets fiercer, the ability to continuously improve is not just a route to efficiency — it's key to survival.
Miro's process mapping tools make it easy to visualize business-critical information and keep teams and stakeholders up to date. Sign up to get started.