You may work in development, logistics, manufacturing, or another type of business with critical machinery. No matter what field you are in, FMEA is a necessary tool for reducing your risk of system failures. Planning out FMEA can be challenging, so we created this comprehensive guide to running a failure modes and effects analysis.
What is FMEA?
FMEA (Failure Mode and Effects Analysis, also known as Failure Modes and Effects Analysis or Failure Mode Effects Analysis), is a procedure used to pinpoint where certain systems or machinery might fail. That way, your team can set up a plan to proactively fix those systems. By reviewing as many components and subsystems as possible, you can identify the system’s potential failure modes and their root causes.
FMEA’s structured approach helps you anticipate potential failures in the manufacturing or design of a product or process. FMEA has two broad categories: Design FMEA (DFMEA) and Process FMEA (PFMEA).
Failures are errors or defects, and can be potential or actual. Failure modes are the ways a product or process fails. (In other words, what went wrong, and how.)
Failure effects are the ways these failures can lead to waste, defects, or harmful outcomes. These consequences could include user injury, machine or process malfunction, or poor product quality. The system failure could also affect other systems directly related to it. Effects analysis studies how failures impact different system components.
FMEA is a common tool used in engineering related to safety, quality, and reliability. The analysis can be qualitative or quantitative. By using inductive reasoning to assess failure risks in a process or product’s design and development, FMEA makes good engineering even better. Your team can use FMEA to evaluate and prevent possible failures by correcting early, rather than reactively—after failures have occurred.
FMEA enables you to identify and prioritize failures according to how serious their consequences are, how often they happen, and how easy they are to find. You can then act to limit or prevent failures, starting with the most serious ones. Find out more.
History of FMEA
Developed by reliability engineers in the late 1950s, FMEA was one of the earliest systematic approaches to analyzing failures and finding their potential causes. FMEA was created to study potential problems caused by malfunctioning military systems, and continues to be effective at discovering potential failures and evaluating system reliability. This allows you to correct and limit process failures early so you can avoid their negative impacts on your system.
Failure mode effects and criticality analysis (FMECA) is an extension of FMEA.
The added criticality analysis lets your team compare the likelihood of failure modes against the severity of their consequences. You can then focus fixes on failure modes with higher probability and more severe consequences, where the fixes can do the most good.
When should you use FMEA?
Ideally, you should begin using FMEA during the earliest conceptual design stages of a process or product, and then through the design or redesign process. Alternatively, you can try using this approach in these cases:
- Before you develop control plans for a new or modified process, and for control before and during ongoing processes.
- When you plan to apply an existing process or product in a new way.
- When you want to improve the quality of an existing process or product.
- For optimal results, you should always examine and improve quality and reliability throughout the life of the process or product.
FMEA greatly benefits business owners and workers
There are also major risks to not using it! Why should you use FMEA? Here are the main reasons people prefer implementing this approach:
Fewer repair costs
FMEA works to proactively repair equipment and systems. So instead of working a machine till it fails and increasing its probability of future breakage, you fix it when it’s most optimal. If the failure is discovered sooner, it costs less than it would later in product or process development, when the failure could be worse.
More uptime
A machine breaks, which slows your assembly line. This means you’re losing money! FMEA procedures allow your team to evaluate design in a straightforward, orderly way, and to identify failure points and system interface problems early. This makes such random breakdowns far less likely.
Greater safety for workers and users
Safety is always your #1 priority, but what if a machine has outdated parts? That could be risky not only for your workers and users but for your business itself. FMEA helps lower risk of injuries through improved design and proactive repair.
Multiple choices for reducing risk
FMEA empowers your team to troubleshoot during ongoing procedures, and to develop ways to monitor performance and locate faults. It’s a documented method that helps you analyze how new or changed designs or processes impact safety and success.
5 industries that use FMEA regularly
FMEA is widely used across industries from software development to manufacturing to healthcare, throughout product or process life cycles. Whatever your business is, discovering failure points early on helps you improve safety and quality, satisfy customers, and save money.
Software development
FMEA can be applied to software development. This approach is usually implemented when the team wants to improve software quality, reduce Cost of Quality (CoQ), Cost of Poor Quality, (CoPQ) and defect density.
Manufacturing
The manufacturing industry counts on FMEA to anticipate and eliminate potential assembly and product failures sooner, and prevent expensive corrective actions later. This results in reliably high-quality products that satisfy industry customers.
Transport and logistics
They also rely on FMEA to empower them to deliver products reliably. The industry uses FMEA to evaluate logistics and supply chains in order to ensure high-quality service to customers.
Healthcare
This industry counts on FMEA as an effective tool for identifying parts of processes that most need improvement. Working preventatively helps reduce risk to both patients and staff.
Agriculture
The industry also relies on FMEA. It is used to assess risk to the environment, to manufacturing and machinery, and to product quality. This is important for environmental, ethical, and legal considerations.
Having trouble putting together an FMEA plan?
FMEA can be complicated to fully plan out, but with Miro’s FMEA template, it’s simple!
We recommend having the template in front of you as you read the rest of this blog post. That way you can fill it out with ease.
Determine your team’s general procedure steps. But first be sure to fully educate relevant team members on your organization’s specific standards for the system you are evaluating. For more about FMEA procedure, read this.
FMEA definitions to get you started
Use FMEA as a risk assessment tool to evaluate the severity, occurrence and detection of risks so you can prioritize the most urgent ones. Read on to learn what each term means. Each category has a scoring matrix with a scale from 1 to 10.
Severity number (S)
Severity numbers are ranked 1–10. Unlikely failures or low risks to the end customer are rated as 1, whereas 10 means a high likelihood of failure or high risk.
Probability of occurrence (O)
The probability of occurrence is how often this failure or problem happens. These are also ranked 1–10, so a failure happening every 3rd time a machine turns on could be rated a 10, while a failure happening every 500,000 times a machine turns on could be a 1 or 2.
Likelihood of detection (D)
The likelihood of detection, also ranked 1–10, shows whether or not you have systems in place to detect the failure. If you get an alert the second a failure happens, mark it as a 1, but if you never get alerts and instead find out on your own, rank it as a 10.
Risk Priority Number (RPN)
Your Risk Priority Number is a combination of the above three. To get your RPN, multiply severity number by probability of occurrence by likelihood of detection: RPN = S x O x D.
How to run a Failure Modes and Effects Analysis with Miro
Now you and your team are ready to begin using Miro’s easy FMEA Template. Simply follow the process steps below.
Step 1. Open up the FMEA Template
You can find the FMEA template in our library. Sign up to Miro free and copy the template.
Step 2. List potential failure modes
What failures have happened over recent years? What are the ways in which the failures occurred? Use sticky notes to write down all the potential failure modes and move them to the area called ‘Detect a failure mode’ on the board.
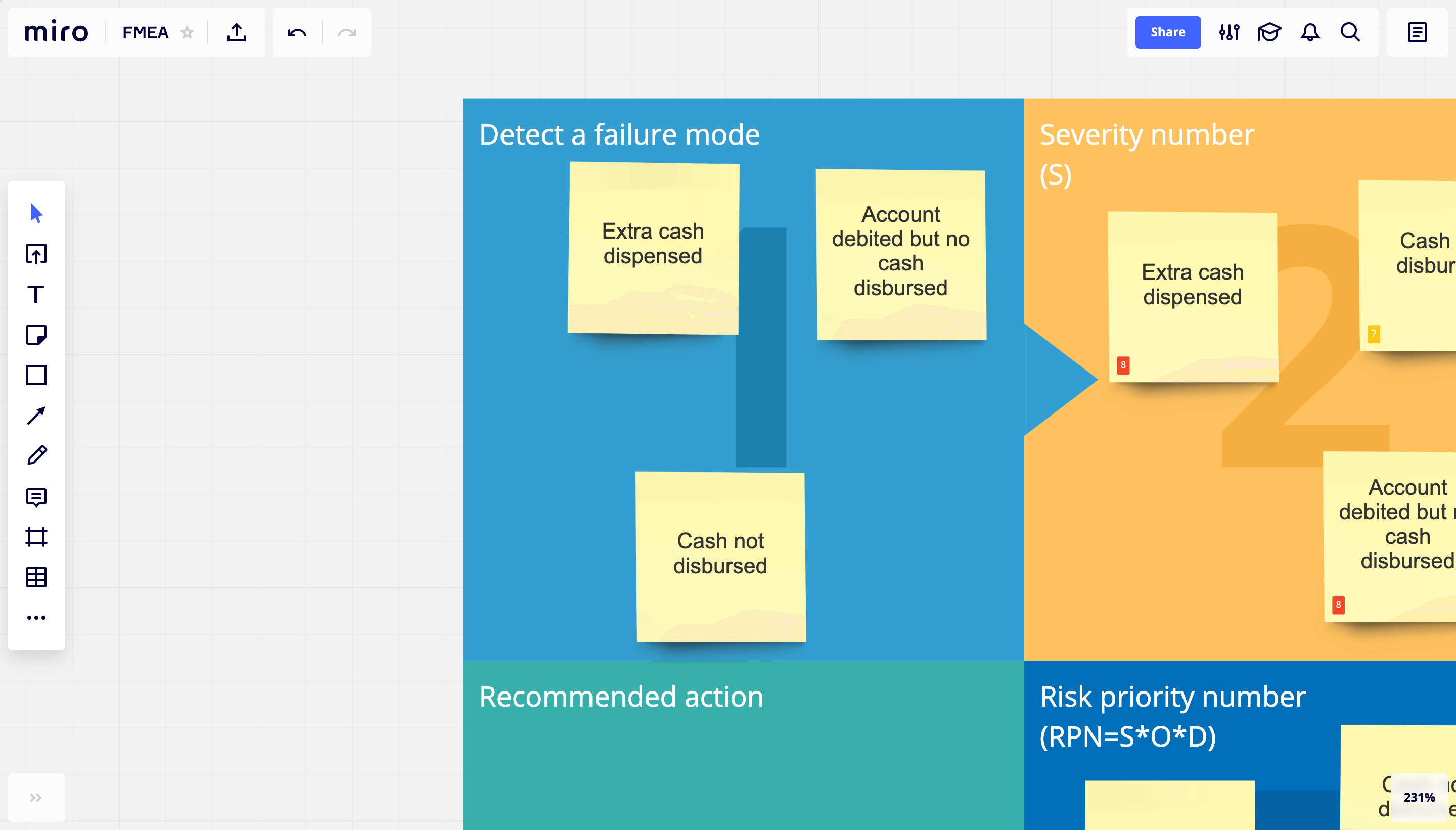
Step 3. Speculate possible outcomes
What is the outcome if a certain system fails? How might each of the process components fail? Record system-wide effects for each failure mode on stickies and put them in the same frame.
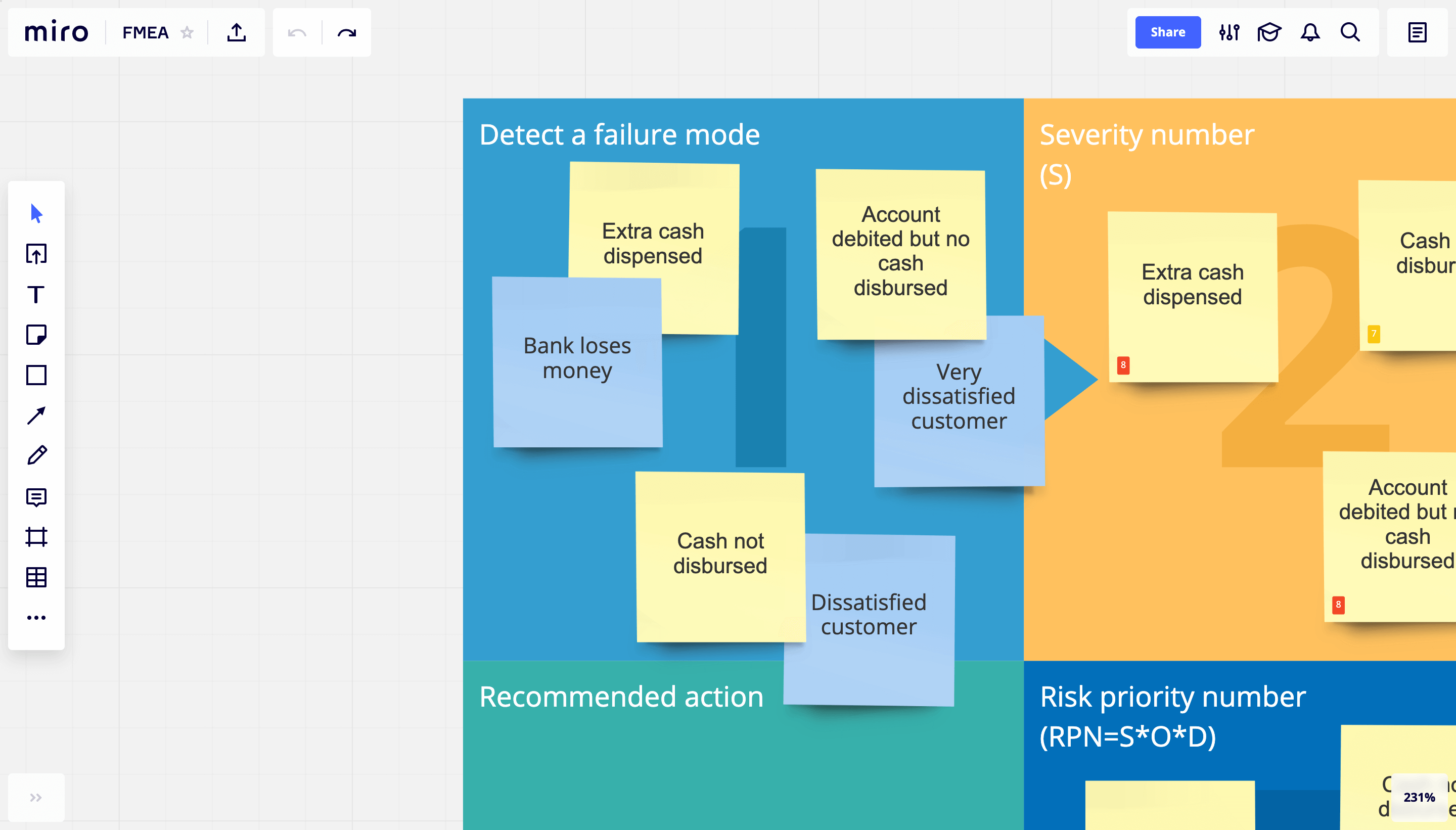
Step 4. Assign S, O, and D rankings
Move your stickies with failure modes to the frame #2 and assign severity numbers. You can create tags and add them to stickies to classify failure modes based on their severity numbers.
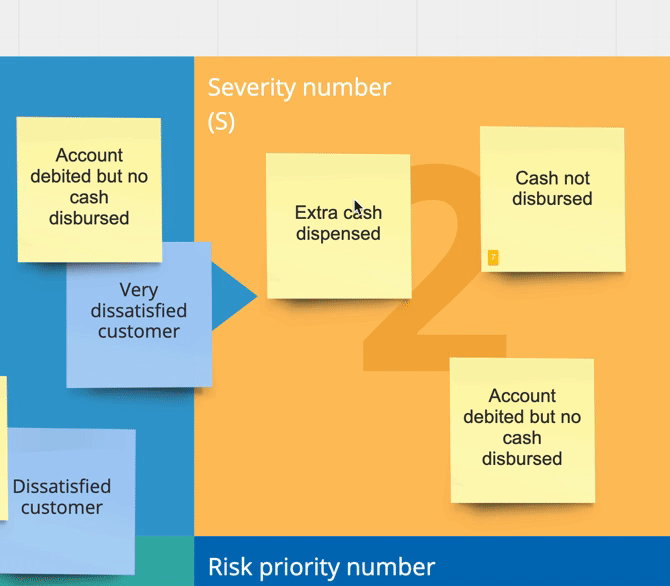
In frames #2 and #3 of the template, assign the probability of occurrence and likelihood of detection using tags.
Step 5. Combine S, O, and D to get the Risk Priority Number
Multiply S x O x D. Once combined, they will give you the RPN. Copy failure modes into frame #5 and add RPN to each sticky.
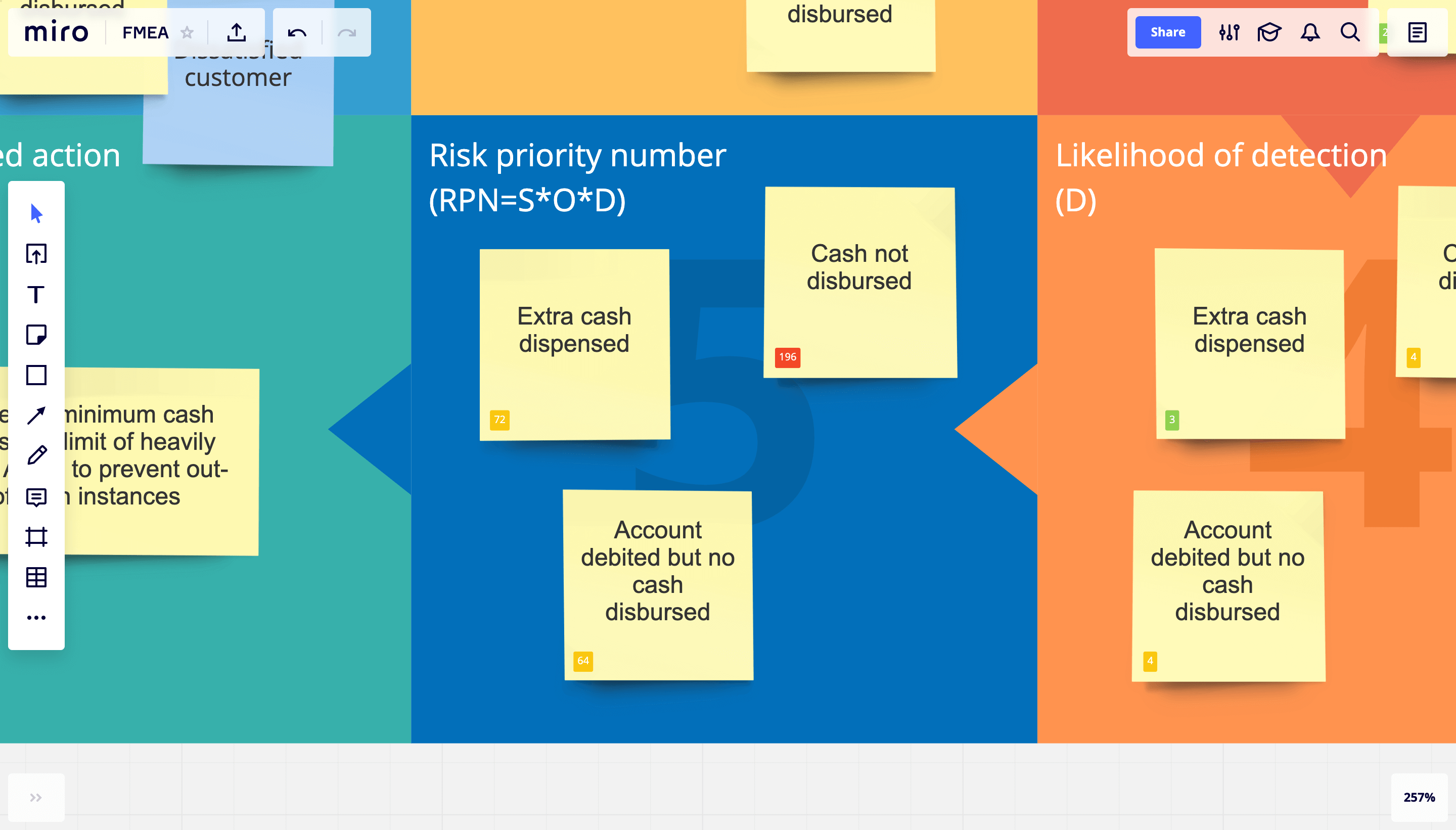
Step 6. Designate which system requires immediate maintenance
Which system has the highest RPN? Remember, higher RPN = more critical, lower RPN = less critical.
Step 7. List recommended actions
Brainstorm scenarios for improving various products or processes. In our example, the most critical failure mode is ‘Cash not disbursed’, so we would list action items for the team to address it.
Step 8. Share your schedule and FMEA
After your FMEA template is filled in, you can share it with all the major stakeholders even if they didn’t participate in the mapping process.
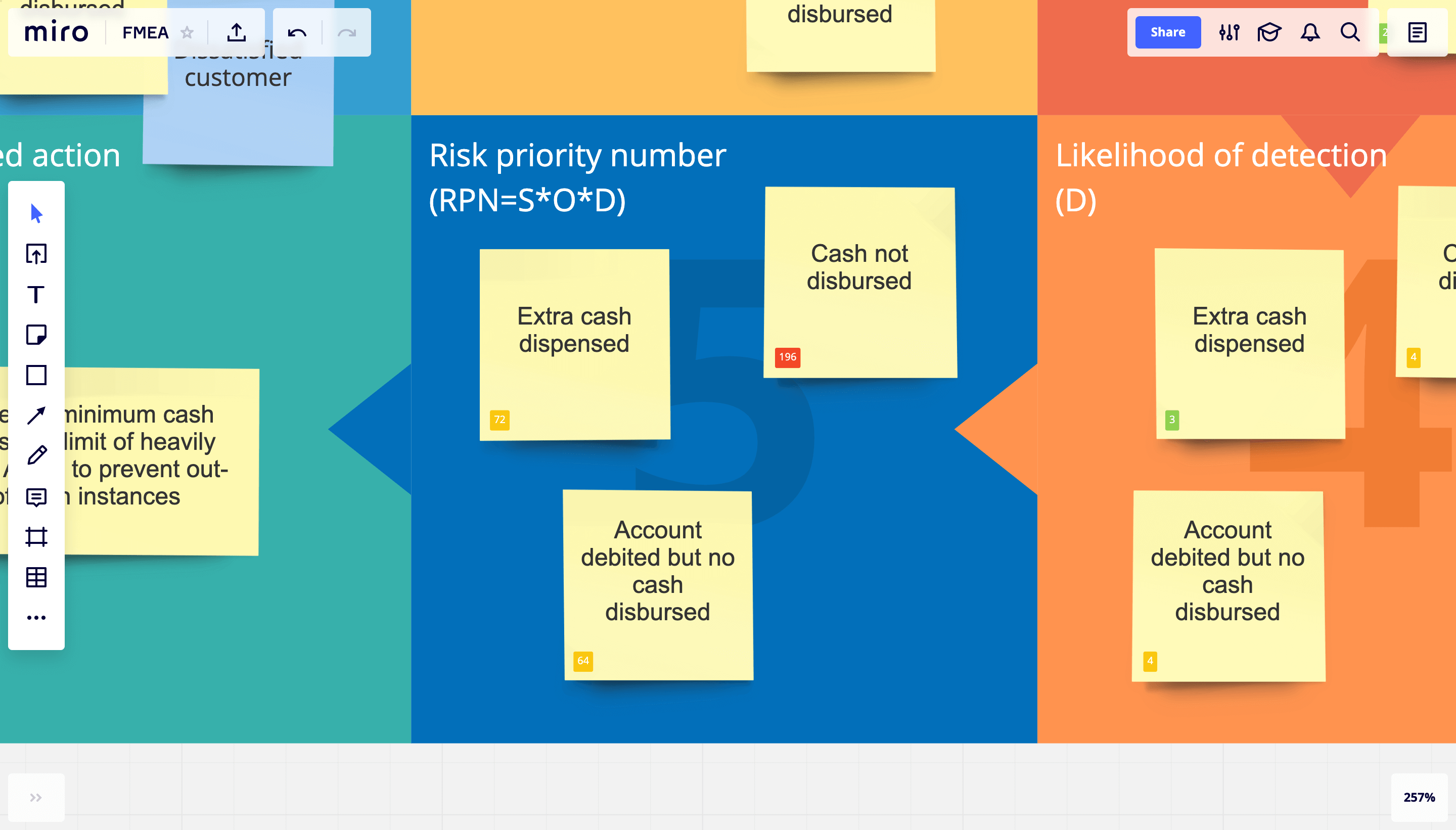
Miro makes FMEA easy
FMEA is a powerful tool that can help your team improve safety, quality, customer satisfaction, and profits. FMEA may seem complicated, but don’t worry! Miro’s template makes the procedure simple.
Pre-made, flexible FMEA templates
Use frames, colorful sticky notes, tags and other features to express and organize your thoughts and issues. These templates enable you to prioritize product or process deficiencies to ensure the best results and satisfy customers. You can also add other templates (such as risk assessment matrix, timeline, or action plan) to visualize the big picture and make the most effective decisions.
Easy document upload
Add visual content including charts, schemes, and pictures to enhance your conceptual presentation. Upload documents and files that can integrate with a wide range of choices such as Google G Suite, Dropbox and JIRA. When you visualize the different components of your product or process, you can better evaluate it with FMEA.
Collaborative tools for members of all different teams
When your team collaborates on a visual whiteboard, you can work together to find and discuss issues. Add comments, refer to each other, and ask questions in video chat to save time and increase productivity. Working collaboratively allows your team to share in contributing to the FMEA process—which means greater improvements, higher quality, and better results!